COMPREHENSIVE ANALYSIS OF HAZARDOUS ENVIRONMENT CLASSIFICATIONS: NEC VS IEC
This article discusses the National Electrical Code (NEC) and International Electrotechnical Commission (IEC) standards, unveiling their underlying principles, technical nuances, and practical applications within the electrical engineering domain.
Introduction:
The threat of fire and explosion is a significant concern in many industrial environments, necessitating a comprehensive approach to risk management. A key element of this approach is the implementation of classifications for hazardous areas or locations, depending on the regional terminology. These classifications are essential for establishing strong safety protocols and complying with relevant standards, thus protecting personnel and equipment from dangers associated with flammable gases, vapours, combustible dusts, and ignitable fibres.
Two major frameworks guiding these classifications are the National Electrical Code (NEC) in the United States and the International Electrotechnical Commission (IEC) standards, widely recognized in the UK, EU, and other regions. In the US, such environments are typically referred to as Hazardous Locations (HAZLOC), while in the UK, EU, and beyond, the term Hazardous Areas is more commonly used.
Defining Hazardous Environments with Technical Specificity
These environments encompass specific spatial domains where the presence of flammable substances, characterised by Auto Ignition Temperatures Temperature (AIT) and minimum ignition energies (MIE), significantly elevates the risk of explosions or fires. Flammable materials fall into three main categories:
- Gases and Vapours: Characterised by a low flash point (the lowest temperature at which vapours ignite) and ability to readily form explosive mixtures with air. Examples include methane, propane, and petrol vapours.
- Combustible Dusts: Composed of finely divided solid particles, these materials can readily ignite and propagate flames in air. Examples include flour dust, wood dust, coal dust, as well as metal dust like aluminium. Notably, sugar dust is also a significant risk, as exemplified by the 2008 Imperial Sugar refinery explosion in Port Wentworth, Georgia. This tragic incident highlighted the severe hazards posed by combustible dusts in industrial settings.
The Imperial Sugar explosion is a well-documented industrial disaster that serves as a stark reminder of the dangers of combustible dust.
- Ignitable Fibres: Composed of natural or synthetic fibres that can easily ignite and sustain combustion. Examples include cotton, nylon, and polyester fibres.
Chemical processing plants, oil refineries, food manufacturing sites, food manufacturing sites, pharmaceutical facilities, furniture manufacturers right the way down to paint and fabrication shops are some illustrative examples, highlighting the widespread presence of hazardous environments across diverse industries regardless of their size or nature. It is paramount to note that the specific explosion groups of the hazardous substances present, categorised based on their explosive characteristics, including flame propagation and explosion severity, are crucial factors influencing the selection of appropriate equipment and safety protocols.
National Electrical Code (NEC) Classification System: A Deep Dive
The National Electrical Code (NEC), promulgated by the National Fire Protection Association (NFPA), serves as a seminal document outlining the guidelines for electrical installations within the United States. The NEC meticulously classifies hazardous locations using a class-division-group schema based on the inherent nature and concentration of hazardous materials, along with their ignition temperatures and MIEs.
National Electrical Code (NEC) Classification System: A Deep Dive
The National Electrical Code (NEC), promulgated by the National Fire Protection Association (NFPA), serves as a seminal document outlining the guidelines for electrical installations within the United States. The NEC meticulously classifies hazardous locations using a class-division-group schema based on the inherent nature and concentration of hazardous materials, along with their ignition temperatures and MIEs.
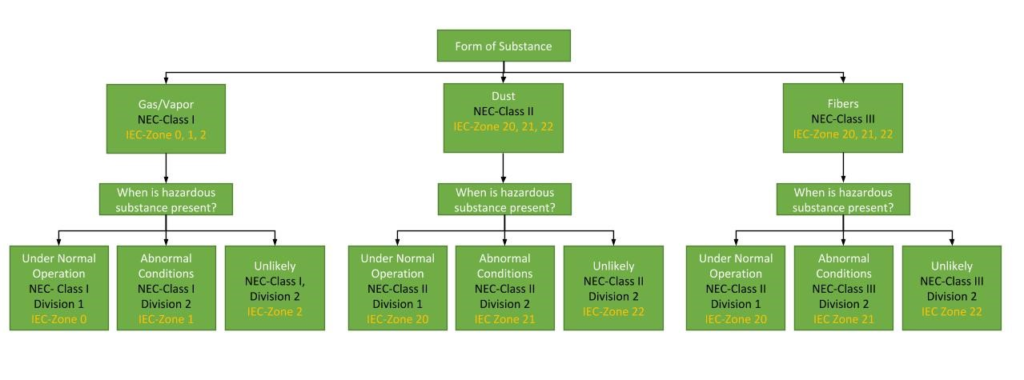
Class-Division-Group Framework: A Technical Breakdown
The Class-Division-Group Framework is a critical classification system used in hazardous area classification. It categorises locations based on the presence and potential explosibility of flammable gases, vapours, or dusts. This system guides the selection of appropriate electrical equipment and wiring methods to prevent accidental ignition sources and ensure safety in these environments.
Class I (Gases and Vapours):
- Division 1: Areas where hazardous gases or vapours are present continuously, periodically, or in periodically frequent quantities under normal operating conditions or during maintenance activities. These areas require the most stringent safety measures due to the high likelihood of encountering flammable mixtures.
- Division 2: Areas where hazardous materials are handled, stored, or used but are not normally present in explosible concentrations. However, leaks, spills, or equipment malfunctions could create flammable atmospheres. Therefore, precautions are still necessary, but they may be less rigorous compared to Division 1.
This framework ensures a structured approach to identifying hazardous locations and implementing appropriate safeguards to minimise the risk of explosions and fires.
Class II (Dusts):
- Division 1: Areas where dust is present in air suspension in clouds under normal operating conditions, or where ignitable deposits of dust are likely to accumulate. These environments pose a significant explosion hazard because the dust cloud itself can become a fuel source. Examples include grain processing facilities, flour mills, and woodworking shops where dust is constantly generated during operations.
- Division 2: Areas where dust is handled, processed, or stored, but are not normally present in air suspension in clouds, and where ignitable deposits of dust are not likely to occur. These locations may still have dust present, but the concentration and potential for ignition are lower. Examples include packaging facilities for dusty products or warehouses storing powdered materials in sealed containers.
Understanding the distinction between Division 1 and 2 for dust hazards is crucial for implementing effective safety measures. Division 1 environments require specialised equipment designed to prevent sparks or overheating, while Division 2 may allow for standard equipment with additional dust mitigation strategies like ventilation systems.
Class III (Fibres and Flyings):
- Division 1: Areas where easily ignitable fibres or flyings are handled, manufactured, or stored, and where such materials are likely to be suspended in air in quantities sufficient to produce ignitable fibrous clouds.
- Division 2: Areas where easily ignitable fibres or flyings are handled, manufactured, or stored, but where such materials are not likely to be in suspension in air in quantities sufficient to produce ignitable fibrous clouds, and where ignitable deposits of such materials are not likely to occur.
Grouping Scheme:
The NEC further categorises hazardous substances into distinct groups (A through G) based on their ignition temperatures, MIEs, and flame propagation characteristics. This grouping system offers a more granular approach to classification, enabling the selection of equipment with appropriate ignition protection levels. Here are some examples of NEC groups:
- Group A: Acetylene (extremely low ignition temperature and MIE)
- Group B: Hydrogen (very low ignition temperature and MIE)
- Group C: Ethylene (low ignition temperature and MIE)
- Group D: Methane, propane (relatively low ignition temperatures and MIEs)
- Group E: Metal dusts (varying ignition temperatures and MIEs)
- Group F: Coal dust (high ignition temperature, but low MIE)
- Group G: Fibres and flyings (variable ignition properties)
It is crucial to note that area classification drawings are often utilised to visually depict the extent (i.e. the size), the shape and classification of hazardous areas or locations within a facility. These drawings serve as vital documentation for ensuring the proper selection and installation of electrical equipment, adhering to safety protocols, and facilitating communication among stakeholders.
International Electrotechnical Commission (IEC) Classification System: Exploring the Zonal Approach
In contrast to the NEC’s class-division-group framework, the International Electrotechnical Commission (IEC) standards employ a zonal framework for classifying hazardous areas or locations. This system focuses on the likelihood and frequency of the presence of hazardous materials, offering a simplified yet potentially less granular approach compared to the NEC.
Zonal Framework: Demystifying the Likelihood of Hazard
- Zone 0: Encompasses areas where an explosive gas atmosphere is present continuously or for long periods.
- Zone 1: Designates locations where an explosive gas atmosphere is likely to occur in normal operation.
- Zone 2: Represents areas where an explosive gas atmosphere is not likely to occur in normal operation but may occur occasionally due to abnormal operations or equipment failure.
While the IEC system offers a more straightforward approach, it is essential to remember that specific technical considerations like ignition temperatures, MIEs, and explosion groups based on explosion severity considerations, are still crucial factors when selecting equipment and implementing safety measures within classified hazardous areas or locations i.e. zones.
Key Disparities and Practical Implications: Navigating the Nuances
While both NEC and IEC offer comprehensive frameworks for classifying hazardous environments, several key differences distinguish them, impacting practical applications:
- Geographical Scope: The NEC primarily finds application within the United States, whereas IEC standards enjoy global recognition, facilitating international trade and harmonisation efforts. For instance, a company exporting equipment from the US to Europe would need to ensure its equipment complies with IEC standards.
- Methodological Divergences: The NEC adopts a detailed class-division-group approach, providing a granular classification scheme that caters to specific types of hazardous materials and their behaviours based on technical properties like ignition temperatures and MIEs. Conversely, the IEC’s zonal framework offers a simpler yet potentially less granular approach, focusing on the likelihood and frequency of hazardous material presence.
- Equipment Selection and Compliance: Selecting and installing electrical equipment within hazardous environments necessitates strict adherence to the relevant classification standards. This includes considering protection methodologies like explosion-proof (EX) equipment, increased safety (Ex e) equipment, intrinsically safe (IS) equipment, purged enclosures, and pressurised enclosures, to mention a few. Choosing equipment with appropriate ratings for the specific hazardous environment, areas, or locations, based on its classification and technical considerations, is crucial for ensuring safety and regulatory compliance.
Conclusion: A Collaborative Approach to Safety in the Face of Diverse Risks
The classification of hazardous environments plays a critical role in safeguarding personnel, equipment, assets and facilities within industrial settings. While both NEC and IEC establish frameworks for achieving this critical objective, their distinct methodologies, areas of application, and technical considerations necessitate a collaborative approach for optimal safety outcomes. By comprehending the nuances of each system and their underlying technical principles, stakeholders can effectively mitigate risks, select appropriate equipment and suitable protection methodologies, and implement robust safety protocols, fostering a culture of safety within hazardous environments, areas, and locations alike.
References:
- National Fire Protection Association (NFPA). (2023). NFPA 70, National Electrical Code (NEC). National Fire Protection Association.
- International Electrotechnical Commission (IEC). (2016). IEC 60079 series: Explosive atmospheres. International Electrotechnical Commission.
- National Fire Protection Association (NFPA). (n.d.). About the National Fire Protection Association (NFPA). National Fire Protection Association.
- My Electrical. (2023, January 23). Hazardous Areas – IEC and NEC/CEC Comparison. My Electrical.
- Fauske & Associates, Inc. (2023, January 25). Hazardous Area Classifications & Information. Fauske & Associates, Inc.
Additional Notes:
- It is important to consult the latest editions of the NEC and IEC standards for the most up-to-date information.
- This article provides a general overview of hazardous areas. It is not a substitute for professional guidance from a competent engineer, consultant or process safety professional.
- When working in hazardous environments, it is crucial to follow all applicable safety regulations and procedures, which applies to the country or region you are operating within.
Want to know more?
Feel free to reach out to Hazardous Area Classification Consultants (HACC) for an informal, yet confidential conversation about your potential hazardous environments, areas or locations.
Email: info@hazardous-area-consultants.com
Tel: +44 (0) 1246 886 380